Personal protective equipment should be one thing above all else: safe. However, how can we guarantee that uvex products actually fulfil the necessary safety criteria? By conducting extensive tests on the material.
Over the past few years we have continually expanded our textile testing laboratory at UVEX SAFETY Textiles in Ellefeld. In part 1 of this blog series you can gain an initial insight into our test equipment – now we also have equipment for testing flame protection in accordance with EN ISO 15025 and a blade cut tester to determine cut resistance in accordance with EN 388.
In addition to standardised test procedures, we are able to use a specially developed test rig to determine the spark resistance of materials, which comes into play in abrasive cutting, for instance.
The individual test procedures at a glance
1. Equipment for testing flame protection
In the standard mentioned above, EN ISO 15025, two procedures are carried out to determine the flame spread behaviour of textiles. Both procedures measure how long a sample continues to burn after the flame has been extinguished. They additionally investigate whether the flame spread reaches the edge of the sample.
a) Test procedure for limited flame spread, Method A – surface ignition in accordance with EN ISO 15025
This test is used for textiles or other industrial products which generally have flame retardant properties or which are intended for this purpose. Six test samples are cut (three along the weft and three along the warp) as defined in the test specifications. The samples are prepared and fixed to the sample holder vertically. The burner is then positioned horizontally and the sample is subjected to a defined flame for ten seconds.
After this, the burner is removed and the sample is assessed according to the following criteria: Continued burning at the edges, afterflame, afterglow, flaming or molten debris and size of holes. The results of the assessment are categorised as set out in Index 1-3. All six samples must meet the requirements. The lowest value is taken as the benchmark for the assessment.
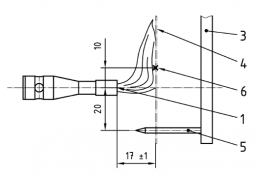
(1) burner
(2) flame
(3) mounting frame
(4) sample
(5) holding pins
(6) aiming point of flame exposure
b) Test procedure for limited flame spread, Method B – edge ignition in accordance with EN ISO 15025
In essence, the same test setup is used for edge ignition as for surface ignition. Unlike surface ignition, however, for edge ignition the burner is placed at a 30 degree angle and impinges upon the bottom edge of the vertically held sample.
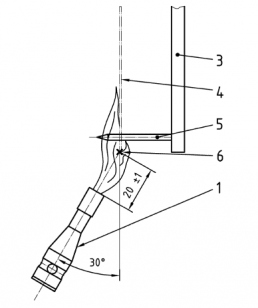
(1) burner
(2) flame
(3) mounting frame
(4) sample
(5) holding pin
(6) aiming point of flame exposure
2. Test rig to assess a material’s spark resistance (Flexstand)
This test procedure is based on a proprietary development of UVEX SAFETY Textiles GmbH. This test procedure was established in tandem with the development of a special coating which protects wearers and clothing against sparks. This testing apparatus enables us to assess the suitability and effectiveness of a material or the coating on a material.
The test rig consists of a mounted and mobile cut-off machine which is pressed against an iron bar at a defined force using hydraulics. In doing so, the rotating cutting wheel creates typical sparks made from tiny molten metal droplets. For this test, a material sample is suspended in the test rig and is exposed to sparks several times in succession. We have defined the distance of the sample from the source of the sparks and the force with which the cut-off machine is pressed into the iron bar in internal test instructions.
This rig enables us to test and assess the spark resistance of a variety of materials. At the same time, we also use the test method for continual quality assurance. As there is currently no standardised test for simulating and assessing material stress during abrasive cutting, this test method is also an excellent complement to the established test procedures for heat and welding standards.
3. Blade cut tester in accordance with EN 388
The standard mentioned actually applies to safety gloves for protection against mechanical hazards. However, the test from this standard to determine cut resistance is also used to assess textile surfaces. In this test, a circular rotating blade is applied horizontally to a test sample in a backwards and forwards motion. A cycle is defined as ten revolutions. The sharpness of the blade is tested on a defined control sample before the test. Five tests are carried out on each test sample. A test is carried out on the control sample between each of these. As a result of this test, the material is assigned a cut resistance level or a performance level. Protection levels are defined from “1 low” (1 or 2 cycles) to “5 high” (20 cycles).
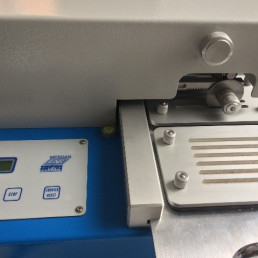
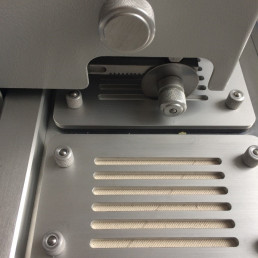