Manufacturing companies across all industries face the major challenge of making their products as sustainable as possible. This also applies to the world of occupational safety, where we at uvex safety have set out to reduce our own carbon footprint more and more. An effort that should pay off. For everyone involved.
One metre and seventy centimetres long, it was discovered by researchers in North-West Australia in 2017: Preserved in rock, the largest footprint ever found on Earth has survived for around 140 million years and is probably silent witness to a sauropod, a giant herbivorous dinosaur. The reliable geological constant in this story is the realisation that anyone who walks on our planet leaves their mark. This was as true in the Cretaceous period as it is today in the Quaternary, for sauropods as well as for humans.
Compared to these periods of time, which are very long by human standards, the study of CO₂ footprints is a rather young discipline. Here, too, we are talking about traces on the planet, but not those measured in metres, decimetres or centimetres. The CO₂ footprint is the result of an emissions calculation or balance of all greenhouse gases released by an activity, process or action. The climate impact of the various greenhouse gases is expressed in CO₂ equivalents, a unit of measurement used to standardise the climate impact of different greenhouse gases. In addition to the unit of measurement, there is another crucial difference: unlike dinosaur footprints, the smallest possible CO₂ footprint is considered desirable.
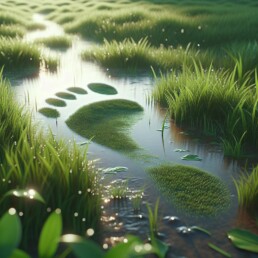
Green electricity in our own plants
For us at uvex safety, calculating our carbon footprint has become a key element in recent years, as Stefan Brück, CEO, confirms: ‘Reducing our ecological footprint has been a top priority for us from the very beginning. At our plants in Germany, we rely exclusively on green electricity and green gas. In our plants in Italy and Sweden, but also more recently in Fürth, we use photovoltaics.’ This has had a ‘very positive impact’ on the carbon footprint of the company, which has been manufacturing personal protective equipment for almost 100 years.
cradle to customer
Production is only one of several levers for reducing greenhouse gas emissions. The raw materials used also play a role, as do transport, sales, trade and, ultimately, use and disposal by the end consumer. The cradle-to-grave principle takes all of these factors into account and calculates the carbon footprint ‘from cradle to grave’. The cradle-to-customer approach, on the other hand, excludes use and disposal, as this is ultimately in the hands of the customer. In Italy, for example, waste is mainly disposed of in landfill sites, whereas in Germany it is often incinerated – resulting in very different CO₂ equivalents for the same products.
This naturally makes comparability difficult, which is why uvex refers to the cradle-to-customer calculation in its own customer communication. ‘We have learnt which factors are responsible for which effects and can now influence the CO₂ value by taking the right measures,’ Brück explains. ‘We calculate these values in all of our product groups and have now created a database that we are really a bit proud of.’
Comparability not only plays a role for potential customers of the products, uvex itself also benefits massively from the growing database. After all, we have set ourselves the goal of operating in a climate-neutral manner by 2045 – five years earlier than the European Green Deal adopted at a political level. And to achieve this, we need a lot of data. Because only those who know their starting level can introduce concrete measures to achieve their target level. The calculation should also be used as a basis for future design and product development processes.
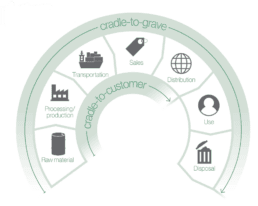
Hemp, corn, bamboo and algae
But what does that mean in concrete terms? To what extent have the products actually changed and are changing? ‘For around five years, we have been developing sustainable PPE in all product categories, some of which is made from bio-based or recycled materials,’ CEO Brück explains. Bio-based, for example, is the renewable raw material of the castor oil plant in the uvex RX cd 5521 planet glasses, where petroleum was previously used. The natural fibres used in workwear are also bio-based: from hemp, maize, bamboo and algae to the already established organic cotton and lyocell. The polypropylene (PP) used for the stems of the uvex xact-fit planet earplugs is recycled, as are large parts of the polyester and PU foam in the climate comfort footbed of the uvex 1 x-craft planet safety shoe.
With all these small material revolutions, functionality is of course still important. The changes would be worth nothing if the safety shoes and safety spectacles were suddenly less safe. PPE remains PPE and must continue to provide the best possible protection. There is no doubt that the uvex credo ‘protecting people’ remains the top priority in product development – but it has now been supplemented: ‘’protecting planet‘ is the consistent continuation of our corporate mission when it comes to dealing responsibly with people, society and the environment,’ Brück explains.
At uvex, all products with the addition planet in their name belong to this generation of sustainable items, but the carbon footprint is not only calculated for these in accordance with the ISO 14067 standard, but also for more and more helmets, respirators, gloves and other items in the entire range. This is an effort that should not be underestimated, as supplier information, among other things, must be obtained in advance in order to be able to efficiently extract output from the SimaPro software using the ecoinvent database. To do this, uvex contacts suppliers, models processes and feeds the resulting data into the system. In-house measurements of waste figures, energy consumption and production figures from the company’s own plants provide additional valuable information in order to be able to calculate the most precise values possible in the end. These all end up on a results data sheet, which is created for each product and contains all the important information. There are no secrets here, instead there is maximum transparency.
Tonnes of savings
For the uvex 1 x-craft planet shoe mentioned above, this results in an amount of 7.43 kg CO₂e. The results become interesting when they can be put into context, as with the uvex 1 G2 planet shoe. Here, the calculated value is 7.3 kg CO₂e, which is significantly less than the comparable standard model uvex 1 G2 with knitted shaft, which produces 8.4 kg CO₂e. Assuming a service life of twelve months, a company with 900 employees could save just under one tonne of CO₂ per year – the equivalent of driving 4,900 kilometres with a mid-range petrol engine.
In view of the high pace of innovation, uvex expects to be able to open up many more such calculations very soon. Specifically, Brück is also thinking about a ‘product cycle concept’. This means, he explains, ‘that we collect our products again after use and either feed them into a recycling process or completely refurbish them for further use. These products are recertified and thus given a ‘second life’.’ The reused product then has less than half the CO₂ footprint. His company will be in a position to present these exciting approaches by the major occupational safety trade fair A+A 2025 in Düsseldorf at the latest.
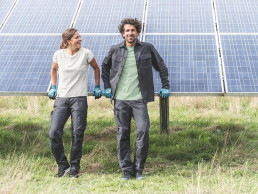
Reducing the carbon footprint is a major goal for uvex, but not the only one, in order to make significant progress in terms of sustainability. In fact, the Fürth-based company has defined four focus areas in which it is investing more heavily. They define how sustainability should be practised in the company today and in the future. In addition to the ecological transformation, which is primarily about reducing carbon dioxide, waste and water, another goal is to utilise the circular economy as a driver of innovation. Materials such as plastics, metals and textiles should be kept in the cycle for as long as possible, thus provoking innovative product solutions. Social responsibility must also be assumed, which is why the plan is to bring about positive change in society and the supply chain through entrepreneurial thinking and action. With the term ecological and health safety in mind, the company also pursues sophisticated pollutant management with the aim of minimising the impact on health and the environment.
‘Sustainability is now part of our strategic orientation,’ Stefan Brück summarises knowing that there is no other way. ‘As a manufacturer, we have a special responsibility here.’ After all, anyone who walks on our planet leaves their mark. And in this case, it is important to minimise them.