Safety footwear protects the wearer against a plethora of dangers. How does it actually work, though? What components and features must a shoe have to provide effective protection against chemical and mechanical hazards? A look inside reveals all!
The basic construction of shoes, trainers and safety footwear is very similar. If we take a cross-section of a safety shoe, it is possible to see the various elements which make up the shoe and their respective functions.
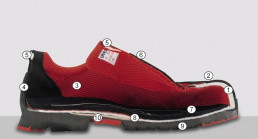
In addition to the familiar and visible shoe components, this view reveals the inner workings of a shoe, offering a glimpse into the particular characteristics of our safety footwear. In the following sections, we discuss the individual components which make up a safety shoe. We will first deal with the shoe upper (1-8), before moving onto the sole (9 and 10).
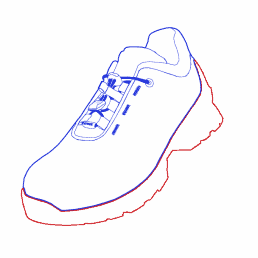
Shoe upper (blue)
- Toe cap ①
Depending on the type of footwear, various toe caps are available which meet different minimum requirements. A protective toe cap on safety footwear must withstand test energy of 200 J under a drop test and 15 kN in a static pressure test. A total of 100 J or 10 kN are mandatory for protective shoes, while occupational shoes do not require caps. Steel, aluminium and plastic caps are currently all used in safety footwear, with the same minimum requirements for all materials. For example, a plastic cap is used in our uvex 1 range. The advantages of this are twofold: firstly, plastic caps are lighter than metal ones and, secondly, they allow a totally metal-free shoe to be manufactured. This aspect is particularly important in certain areas, for example in airports.
- Upper material ②
In addition to an assortment of leather types (smooth, nubuck and split leather), textiles and synthetic materials are also used. For example, our uvex 1 range features micro-velour. The different characteristics determine the use of the respective materials for various applications. These include, but are not limited to: breathability, non-slip, water permeability, weight, price, allergy risk, heat conductivity, fire resistance and cleanability. For example, micro-velour is considerably more breathable than either smooth or nubuck leather, whereas leather performs somewhat better in terms of stability.
- Lining material ③
The shoe lining is in direct contact with the foot inside the shoe. The lining material therefore fulfils important tasks such as guaranteeing breathability, water vapour permeability and absorption, climate control and quick drying capacity, as well as high levels of rub and abrasion resistance. In addition, it should feel comfortable for the wearer. Various materials are also used for this purpose: leather, textiles, thermo-regulating textile materials and membranes.
- Heel cap ④
In order to offer the best possible protection against going over on the ankle and to facilitate a pleasant fit, the rear of the shoe features what is known as a heel cap. This can be made from card, bonded leather, thermoplastic foil or thermoplastic rubber. Shaping the outsole is also possible, which would then replace the heel cap inside the shoe. As the picture shows, the uvex 1 features the latter. The advantages of these formed caps are in the anatomic heel design and consistent quality.
- Padding ⑤
The collar and tongue area are softly cushioned. This helps evenly distribute the pressure generated from the lacing system across the instep and to improve wearer comfort at the shaft. It is important to use soft, yielding materials, particularly in the area surrounding the Achilles tendon, so as to avoid irritation.
- Lacing ⑥
The shoe cross-section shows the elastic lacing system. This has the advantage of being quick and easy to fasten, staying in place all day without needing to be retightened. The elastic laces also offer greater flexibility over the course of the day as they expand if the feet swell up, which eases pressure. In addition to elastic fast lacing systems, more traditional shoelaces are also common in safety footwear.
- Removable insoles ⑦
A removable insole is fitted above the insole. Depending on the design of the removable insole, this provides additional shock absorption at the heel or front of the foot, as well as a partial support for the arch of the foot. The removable insole is breathable, ensuring that any humidity and moisture are removed from the shoe. It has a pleasant, non-irritating surface structure and dries quickly. A wide-range of materials can also be used, including foams and non-woven materials.
- Insole ⑧
The insole forms a connection between the shaft and the sole. As far as materials are concerned, pulp fibres, leather or non-woven materials can be used. The insole’s principle function is to ensure contact resistance, while additionally removing moisture and enabling the shoe to dry quickly. The non-woven insole favoured by uvex is also pH neutral, skin-friendly and excels through consistent antistatic properties.
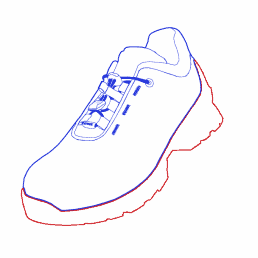
Sole (red)
- Outsole ⑨
Outsoles are typically made from polyurethane (PUR), thermoplastic polyurethane (TPU) and rubber (nitrile rubber). These materials can be differentiated according to their characteristics. In order to choose safety footwear that offers the best protection for a particular area of application, these characteristics should be considered. We use PUR in both the midsole and outsole for our uvex 1 range, which is directly injection moulded to the shaft in a special process. In basic terms, the differences between rubber and PUR are heat and chemical resistance properties, with rubber soles offering greater resistance. Shoes with rubber soles are therefore the correct choice for areas of application in which these kinds of hazards may arise. Given that the uvex 1 range was developed with lightweight applications in mind, other characteristics come into play: for instance, the midsole is made from a PUR foam as it is lighter than rubber (and even compact PUR), while also offering the wearer significantly improved shock absorption.
- Midsection with insert for ladder support ⑩
The midsection is designed to provide stability to the middle of the foot for standing on ladders safely. In order to avoid related wear and tear, the midsection joint area on the sole is furnished with a highly abrasion-resistant and non-slip PUR component.
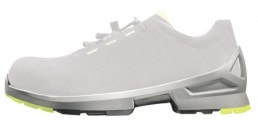
Although this is not the case in our pictured cross-section, some models include penetration-resistant insoles and scuffcaps over the toe cap:
- Penetration-resistant insoles
Penetration-resistant insoles come in steel or textile variants. Here, too, the same demands are placed on both product types: penetration-resistant metal and textile inserts must be able to resist penetration from a test nail with a diameter of 4.5 mm under a specific force of 1.1 kN. Steel inserts are placed between the insole and the outsole. A penetration-resistant textile insert usually replaces the existing insole. This is just one of the differences between the two materials.
Given that steel inserts are manufactured in standard sizes and are not specially adapted to individual models of shoes, some areas around the edges of the insole may remain unprotected. Conversely, a textile insert replaces the insole. This means the entire foot is protected. It is also more lightweight, more flexible and prevents cold bridges between the cold floor and the shoe inner. However, the steel insert has the advantage of being resistant even to thinner nails. Steel is the material of choice in the construction industry, where the danger of sharp objects being misplaced is relatively high.
- Scuffcaps
The scuffcap: although not in our profile, it plays an extremely important role in safety footwear for other application areas. Various types of leather, carbon-reinforced leather, foam PUR and thermoplastic PUR (TPU) are used for scuffcaps. The fundamental role of the scuffcap is to protect the outer material on the toe cap from mechanical stress. It thereby reduces wear and tear of the material and extends the service life of the shoe. While foam PUR and TPU are more abrasion-resistant, (carbon-reinforced) leather has a greater degree of heat resistance.