The health and safety of employees should be the top priority in any company. To ensure that safe environments are maintained throughout the business, employers’ liability insurance associations carry out regular site inspections for an in-depth evaluation of the company’s occupational safety. When an employers’ liability insurance association announces that it is time for an inspection, it usually causes a certain amount of anxiety. In this blog post, we explain what to expect from site inspections and show you why there’s no need to fear them.
Why are health and safety inspections carried out?
As German Social Accident Insurance (DGUV) policyholders, employers’ liability insurance associations are required to ensure that occupational health and safety is maintained within companies in order to reduce the risk of accidents at work to a minimum. Regular site inspections are therefore obligatory for every employers’ liability insurance association. There may also be other reasons for a health and safety inspection:
- A change of workplace or new equipment
- A hazard class is due to be assigned
- A complaint about the company has been lodged with the German Social Accident Insurance
- An employee has been involved in an accident
- To meet the technical supervisor responsible for health and safety
- When statistical data needs to be compiled
The law does not specify how frequently health and safety inspections should be carried out – but they should be conducted regularly, according to the German law on occupational safety (“ASiG”). What “regularly” actually means depends on the size of the company and its level of risk. In any case, an inspection should be carried out at least once a year, as this is the only way to ensure that the objectives of the law on occupational safety are met.
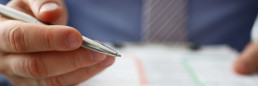
What does a health and safety inspection by an employers' liability insurance association involve?
A health and safety inspection conducted by an employers’ liability insurance association always consists of an initial briefing, an inspection of the site and a debrief. The following people should be present throughout:
- The company director
- Individuals responsible for health and safety
- Occupational safety expert(s)
- An occupational health doctor
- At least one employee representative from the works council
- The managers of each department
The initial briefing
During the initial briefing, a quick risk assessment for each area is discussed first. There is also a general conversation about occupational safety, accidents at work and the latest developments in occupational health and safety. It is therefore a good idea to gather together all the relevant documents that the inspector will want to see ready for this briefing.
Site inspection checklist
You should provide the following documents for a health and safety inspection by an employers' liability insurance association:
- Risk assessment
- List of hazardous materials
- Operating instructions
- Safety data sheets
- List of required personal protective equipment (PPE)
- Skin protection plan
- Emergency and evacuation plan
- Test reports relating to fire protection, life-saving equipment, electrical systems and equipment
- Accident log, evidence of first aid provisions
- List of work materials and equipment
- Assignment of employer responsibilities
- Written appointments of safety specialists, occupational health doctors, safety officers, company first aiders etc.
- Written contracts for forklift trucks, crane operation etc.
- Evidence of occupational health screenings
- Regulations for external staff, temporary staff, trainees etc.
- Documentation relating to initial and ongoing training
The inspection
During the site inspection, the inspector will check the individual work areas for hazards and establish whether these have been recorded in the risk assessment and are managed appropriately. The following factors are checked for potential risks:
- Mechanical hazards – e.g. corners, edges, sharp points etc.
- Electrical hazards – e.g. equipment that carries live voltage
- Chemical hazards – e.g. poisonous substances in the air
- Biological hazards – e.g. from plants, animals or microorganisms
- Fire and explosion hazards
- Thermal hazards – e.g. hot or cold surfaces
- Physical hazards – e.g. noise, radiation, pressure etc.
- Physical strains – e.g. posture during work
- Psychological stressors – e.g. workflow, activity, working conditions etc.
- Working environment – e.g. temperature, lighting, furnishings etc.
- Awareness and management
- Organisation, cooperation and qualification
The inspection of technical areas is carried out by technical supervisors. These are trained scientists, engineers and master technicians.
Sometimes, only certain parts of the different work areas or certain employee groups can be investigated in the course of a site inspection – in these cases, the investigation is known as a spot check.
Any shortcomings identified during the inspection are recorded in a protocol.
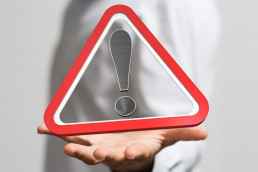
The debrief after the health and safety inspection
After the inspection, there is a review in the form of a debrief. This involves an in-depth discussion about the protocol in which any hazards or shortcomings have been recorded and how these might be eliminated. The site inspectors will determine how each problem should be rectified and will set a deadline by which this must be achieved. The employers’ liability insurance association will then arrange a follow-up visit to check that the hazards have been taken care of as discussed. The occupational safety experts and company directors are responsible for making sure the changes required as a result of the site inspection are implemented. The heads of each department must also be informed about the problems identified. It is best practice to record all the issues discussed and the deadlines for each action point in your own protocol – if no follow-up visit has been agreed, you can assume that the next health and safety inspection will take place immediately after the deadline. That’s why it is important to take the identified shortcomings very seriously and rectify them as soon as possible.
Do you feel well-prepared for your next health and safety inspection with your employers’ liability insurance association? We’d love to hear about your experiences of site inspections at your company. Do you have any tips for other businesses? You can find more information about accidents at work and employers’ liability insurance associations in our blog post: “Arbeitsunfälle vermeiden – Dank BG Zuschuss für Ihre PSA – Bis zu 50% Förderung” (Preventing accidents at work – get financial help for PPE from your employers’ liability insurance association – grants of up to 50%).