When it comes to safety, you shouldn’t leave anything to chance. That’s why strict quality criteria are applied to all uvex safety personal protective equipment (PPE) products. But how can we guarantee that they meet the necessary requirements? With lots of material tests!
Join us as we take a look at our textile test laboratory in Ellefeld, where both ready-to-wear clothing and the textiles and raw materials used to make it are put through their paces using various test methods. Led by garment technologist Svenja Müller, the laboratory specialises in carrying out physical tests and quality assessments. For example, textiles can be tested in the laboratory to determine their tear or flame resistance, as well as their dimensional stability when subjected to frequent washing and drying.
What kind of test methods are used?
Textiles used to make protective clothing have to withstand mechanical stresses caused by
- tension
- pressure
- bending
- friction
- heat and even
- flames and fire
The decisive factor in determining which fabrics and materials are suitable for uvex safety products are values determined during various, mostly mechanical, test methods in accordance with industry standards. Based on these, the properties of various types of textiles and raw materials can be compared with each other, with only the best used for developing uvex safety protective workwear.
In the following article, we outline the six most common test methods used at the textile testing laboratory in Ellefeld, Saxony.
This mechanical test method is used for woven textiles, laminates and nonwovens. According to the test specification, a total of ten samples of a particular textile are to be subjected to this test. The samples are cut into strips and clamped in a traction machine in such a way that five strips each are subjected to the traction force lengthwise and crosswise. Using a predefined tensile speed, each sample is stretched until it breaks – in other words, until the textile fibres yield to the load and tear off.
The measured maximum tensile force corresponds to the maximum tensile force recorded during a test. The result is given either as the mean value of the lengthwise and crosswise test samples or the lowest value measured.
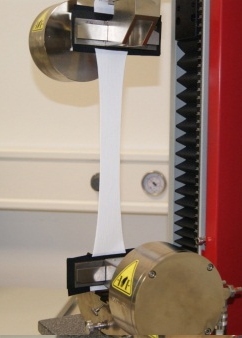
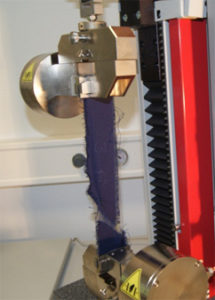
Tear propagation resistance is usually determined by one of two methods: firstly, the trouser-shaped specimen tear propagation test for textile fabrics, i.e., woven and braided fabrics, knitted fabrics, felt, mesh, netting, stitch-bonded fabrics etc. or secondly, the trapezoid method for nonwovens and laminates.
In both test methods, a total of ten samples of each material type are tested in both a lengthwise and crosswise direction. They should be cut according to the respective standard specification in such a way that either two trouser-shaped specimens or a trapezoid are produced.
The tensile force that needs to be applied to cause crack propagation – i.e., tear propagation – is determined. This is particularly relevant in assessing the extent to which a piece of personal protective equipment can still offer protection after it has already been damaged. The result is given either as the mean value of the lengthwise and crosswise test samples or the lowest value measured.
This textile fabric test method uses a strip test. The samples are laid out as straight strips or in loops to test their elasticity – i.e., the extent to which the fabric can return to its original state after it has been stretched considerably. Elasticity plays a major role in a garment’s shape retention properties, for example. If it is not elastic enough, wearer comfort can be considerably affected – which may in turn reduce the wearer acceptance of important safety clothing.
Again, a total of ten samples (five lengthwise and five crosswise) are subjected to the test and cut according to the respective standard specification. The result is given either as the mean value of the test samples or the lowest value measured.
Especially for protective clothing, high abrasion resistance is a great advantage. The Martindale method is most often used to determine this. It recreates the natural wear and tear of a fabric by rubbing circular samples of the textile against an abrasive under fixed load (9 or 12 kilopascal). A specifically designed wool fabric is used as the abrasive, which is clamped on an abrasion bench.
The method provides information on how many abrasion cycles a material can withstand: the test is repeated at specified intervals until all test samples are destroyed. This is the case as soon as two threads of the textile are completely worn out, which is evaluated using a magnifying glass. The result – the wear number given in Martindale – is taken from the lowest value from four samples. The higher the wear number, the longer the material can withstand mechanical stress caused by abrasion.
This test method determines the extent to which the dimensions of a textile product change following typical washing and drying procedures. To start, initial measurements are taken, then the samples are washed and dried according to the washing and drying instructions. Re-measurement and subsequent comparison of initial and final dimensions give the dimensional change as a percentage.
This test is also used to determine – and improve – a garment’s shape retention properties. Only when protective clothing fits perfectly can it provide its full protective effect. However, if it wears out after a few washes and has to be replaced frequently, this is a cost factor that shouldn’t be underestimated for companies that have to provide PPE for their employees.
a) Test method for limited flame spread: method A – surface ignition according to DIN EN ISO 15025
For this test, six specimens (three lengthwise and three crosswise) are cut to size according to the test specification, prepared and attached vertically to the specimen holder. The test laboratory personnel then set up a burner in a horizontal standby position and expose the samples to a defined flame for ten seconds each.
The burner is then removed and the sample assessed according to the following criteria:
- Does the fabric continue to burn all the way to the edges?
- How long is the afterflame time?
- How long is the afterglow time?
- Are there any flaming or melting droplets?
Based on the assessment, the fabric is ranked on a scale from 1 to 3. Each of the six samples must pass the test; the benchmark for the evaluation is the worst value in each case.
b) Test method for limited flame spread: method B – bottom-edge ignition according to DIN EN ISO 15025
The test set-up used as for surface ignition is generally also used for bottom-edge ignition. However, for bottom-edge ignition, the burner is directed at the lower edge of the vertically mounted sample at a 30-degree angle. The results are evaluated in the same way as for method A.
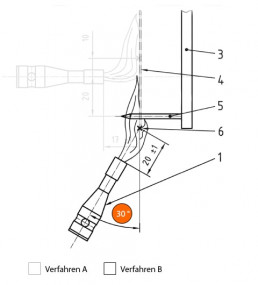
(1) Burner, (2) Flame, (3) Mounting frame, (4) Sample, (5) Retaining pins, (6) Guide point of the flame effect
Especially in dangerous situations, it’s crucial to be able to rely on the flame-retardant properties of PPE. This is necessary for fire brigade operations, for example. Here, fireproof protective clothing is required to ensure the safety of the rescue workers.
The DIN EN ISO 15025 standard describes two methods of determining the flame spread properties of a flame directed at textiles. Both methods involve measuring the time that the sample continues to burn after the flame is removed. They also include a check to see whether the flame spreads to the edge of the sample.
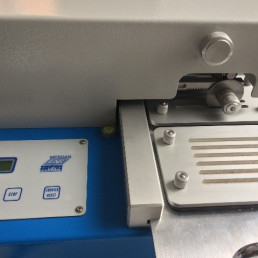
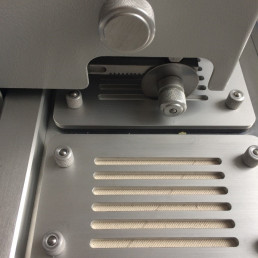
This standard applies primarily to safety gloves that are intended to protect hands from mechanical risks. The main focus is on protecting the hands and fingers from cuts, but the test method can also be used for textile fabrics, because other parts of the body also need to be protected from cuts by suitable protective clothing in certain work situations.
The cut resistance of a material is tested in each case by means of a round, rotating blade that moves horizontally back and forth on a control sample. Each cycle consists of ten rotations. Before the test, the sharpness of the blade is checked on a specified control pattern. Five tests are carried out on each test sample – in between, one test is carried out on the control sample. Based on the results of the test, the material is assigned a cut protection or performance level. Protection levels range from 1 (low – withstands 1 or 2 cycles) to 5 (high – up to 20 cycles).
In addition to these standardised test methods, the Ellefeld test laboratory has its own specially developed test stand that can be used to determine the resistance of fabrics to flying sparks. Flying sparks are caused by certain types of work, such as cut-off grinding, where tiny pieces of glowing metal swirl through the air and may result in skin injuries if proper PPE is not worn.
There is currently no standardised test method for spark resistance that authentically simulates and evaluates the material stress involved. The flying spark test method has therefore been developed in house by uvex safety while creating a special coating for fabrics. The test set-up allows the suitability and effectiveness of this coating on a fabric, or of the fabric itself, to be evaluated.
The test stand consists of a mobile mounted cut-off machine that is hydraulically pressed against an iron bar under a defined pressure. The rotating cutting disc produces the flying sparks typical of cut-off grinding. For the test, a fabric sample is clamped in the test stand and exposed to sparks several times in succession. The distance between the sample and the spark source, as well as the pressure with which the cut-off machine rests on the iron bar, is defined in an internal test routine.
The Flexstand is used to research how new materials react to flying sparks. The materials are evaluated and grouped according to the test result. The test method is also used for the ongoing quality assurance of materials already in use. The test stand is an excellent addition to the standardised and established test methods for heat and welding protective clothing.
The Ellefeld test laboratory uses the test methods described above to ensure that uvex safety PPE reliably does what it’s supposed to do. The specific properties of raw materials are tested in the lab. The results of these tests can be used for competitive analysis and to assure the quality of the finished products. In addition, the knowledge gained of course also serves as a basis for the continuous development of uvex’s diverse protective clothing product range.
The textile testing laboratory and its testing expertise are also continuously being developed and updated in line with the latest technological developments. And we’ll keep you updated in our blog about all the latest innovations in the testing methods we use.